Toolroom
Introduction
Plastic Blow & Injection Mold Design and Manufacturing.
Esteplast has its own in-house facility for the fabrication of Molds, Tools and Spare Parts of Machines & Molds. Having an in-house toolroom provides a significant advantage by enabling quick maintenance and repair of molds & Machine components. This ensures minimal production downtime and helps us to meet delivery commitments to our valued customers efficiently.
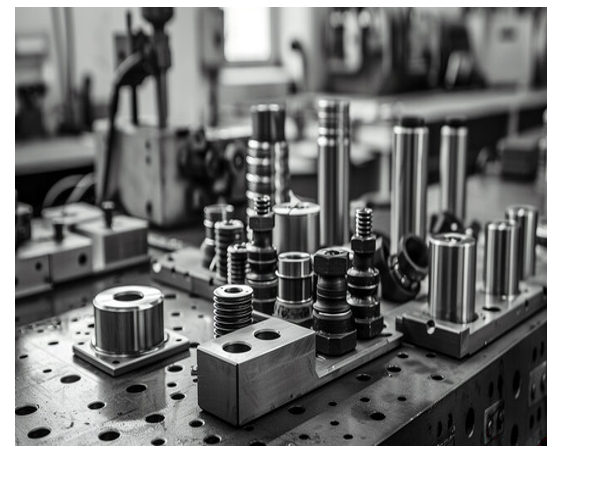
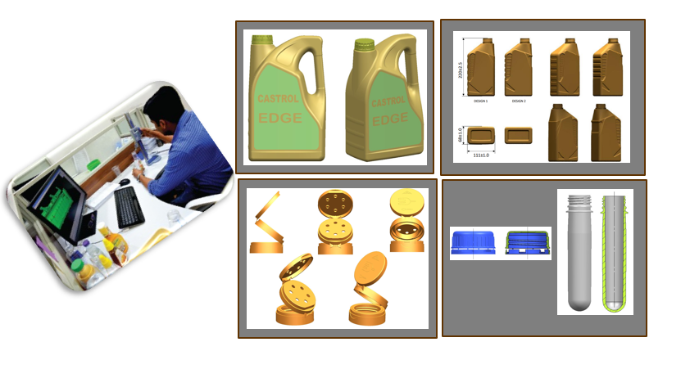
Designing Process
Facility Designing Process:
Our 3D facility design process enables detailed visualization of manufacturing layouts, ensuring
optimal space utilization and streamlined workflows.
Additionally, the 3D design provides our valued customers with a realistic representation for initial approval, facilitating better decision-making and alignment with their expectations.
Prototype Development
Prototype Development & Approval Process:
To drive innovation and ensure product excellence, we have integrated a plastic bottle prototyping process within our operations. This allows us to develop and refine new bottle designs before full-scale production. by leveraging our in-house prototype machine, we can quickly validate design concepts, approval process to ensures that prototypes meet customer specifications..
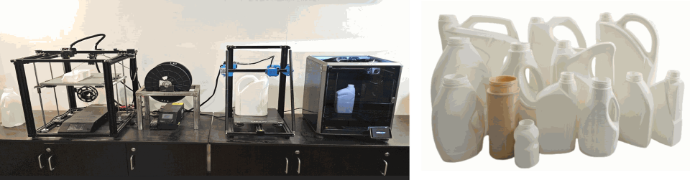
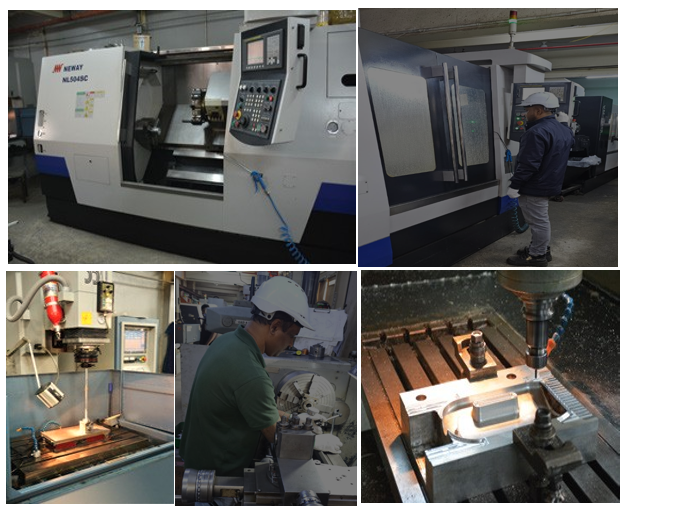
Tooling Facility
our toolroom is equipped with highly precise machinery, allowing us to maintain the highest standards in mold design, manufacturing, and maintenance. This capability not only enhances production efficiency but also ensures consistency and quality in our products.
- 3D printer
- CNC Milling Machine
- CNC Lathe Machine
- Lathe Machine conventional
- Milling Machine Vertical
- Milling Machine Horizontal
- Drilling Machine
- Sand Blasting Machine
- Hydraulic Press Machine
- NC EDM Machine
- Surface Grinder
- Proto Graphic Machine
- Hardening Facility
Blow & Injection Mold
Our mold design process begins with 3D CAD modeling and simulation, allowing for precise engineering and mold flow analysis. Using high-quality materials, CNC machining, and EDM technology, we manufacture molds that deliver consistent product quality, minimal waste, and high efficiency.
Our experienced team ensures every mold meets stringent industry standards. We integrate modern cooling systems, precision cavity design, and automated systems to enhance cycle time and productivity.
Successfully innovated the mold cooling system by transitioning from an external cooling setup to an internal cooling system. This enhancement has improved thermal efficiency, reduced cycle times, and optimized mold performance, leading to better product consistency and energy savings."
With our commitment to innovation and quality, we provide reliable solutions for plastic bottle manufacturing, caps, and other injection-molded components
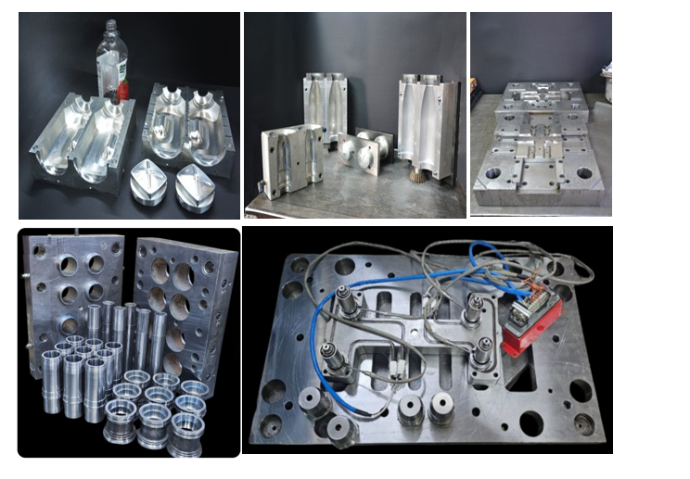
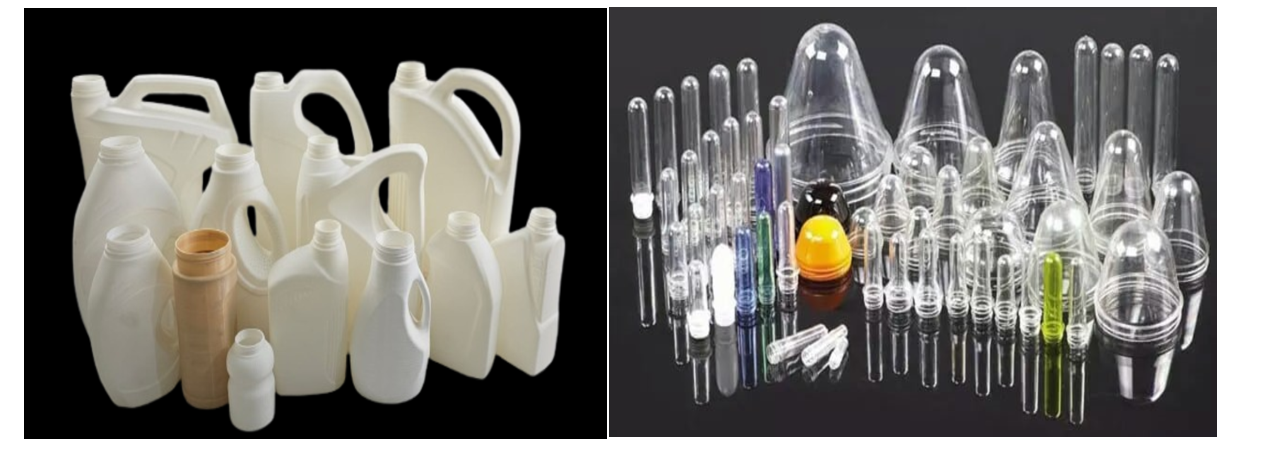